Physical Dimensions
Width 620 cm
Depth 626 cm
Height 760 cm
Weight 56 Kg
Build Volume
Width 300 mm
Depth 300 mm
Height 300 mm
Lightweight Cable with Digital Temperature Measurement
The Pro3 Series replaces the drag chain cable with a lightweight cable, to reduce the weight of the extruder and keep the center of gravity in the middle during printing for more stable print quality.The Pro3 Series also uses digital temperature measurement, for an accurate temperature reading to help prevent jamming.
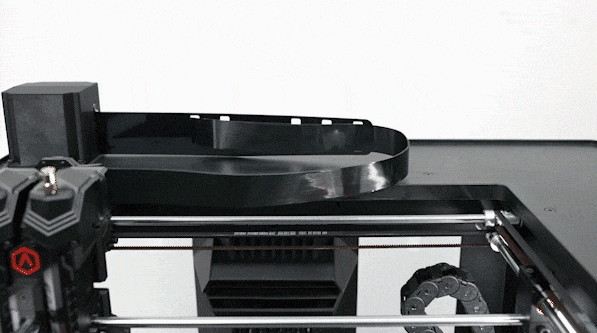
The importance of Auto Bed Leveling
Bed leveling is the process of confirming that the printing platform is as level as possible. The Pro3 Series has this leveling procedure as an automated function. Auto bed leveling will maintain the distance between the print nozzles and the bed, to create a uniform build area. This improves bed adhesion and allows the nozzle to adjust to even the most minor surface contour changes.
.gif)
Live Monitoring HD Camera
The Pro3 Series uses a HD camera to monitor the entire 3D printing process of every print job. This camera operates by connecting to RaiseCloud, allowing users to keep track of every print job remotely and while on the move. This ability to check the 3D printing process gives peace of mind. The Pro3 Series also comes with an upgraded CMOS sensor to ensure better image quality.
Power Loss Recovery
Either a power outage or a filament outage (when the filament runs out) can cause a print job to be lost if they occur in the middle of the 3D printing process. However, the Pro3 Series has a filament run-out sensor on its extruders to alert when the filament is about to run out and saves the print job. It also has a second-generation power loss function to save the printing status in the event of a power outage and can continue printing from the same point when power is restored.
The Pro3 Series is compatible with a variety of 3D printing materials (known as filaments) to meet project requirements
Depending on the project goals, more than one 3D printing filament is necessary to accommodate varying structural or functional requirements (for example, some requirements may include flexibility, and strength). Sometimes multiple filaments are required within the same print job. Having a 3D printer that is compatible with different filament types is both cost-saving and practical for print jobs requiring multiple filaments, giving it extra versatility other printers cannot match.